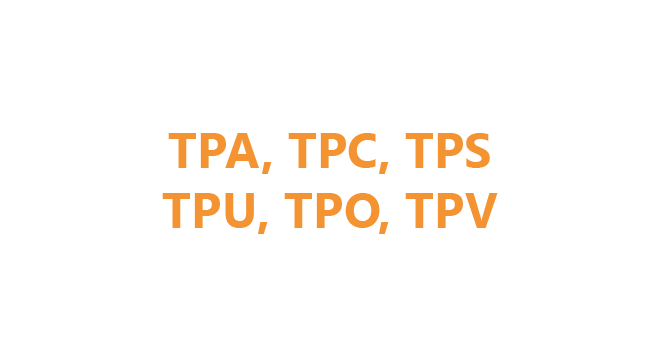
Thermoplastic elastomers
Thermoplastic elastomers (TPE) are compounds that combine the elasticity, appearance and feel of conventional thermosetting rubber with the processing efficiency of thermoplastics and can be tailor-made for versatile applications.

Abbreviation
TPE
Molecular formula
C26H20
CAS no.
632-51-9
General description
Thermoplastic elastomers are copolymers that can be deformed by heating and, when heated, can be easily processed by standard techniques such as injection moulding. Unlike other, stiffer materials, thermoplastic elastomers can be stretched and return to their almost original form, which has a positive effect on service life and physical properties.
The manufacturing process of TPE is reversible. Therefore, the products can be reprocessed and reshaped, provided that only single varieties are collected together.
The TPE materials achievable through various blends are like vulcanised rubbers in many properties but can be formed and extruded using traditional thermoplastic processing equipment. This is an important advantage, as thermoplastic processing is more cost-effective and is characterised by significantly shorter cycles.
Definition
Thermoplastic elastomers are plastics that behave comparably to classic elastomers at room temperature. When heat is applied, the thermoplastics can be deformed. Since a wide variety of combinations of different thermoplastic components are produced, this leads to a large variety of TPE plastics, which are classified according to DIN EN ISO 18064 depending on their chemical-morphological structure.
Thermoplastic polyamide polymers (TPA) have a hard component of polyamide-6 or polyamide-12 monomers that form blocks in the polymer chain and alternate with soft components comprising polyether or polyester units. TPA are block copolymers.
Thermoplastic polyester polymers (TPC) are multiblock copolymers in which different polyester units alternate with each other or polyester units with polyether units.
Thermoplastic styrene polymers (TPS) are copolymers made of styrene-isoprene or styrene-butadiene units, which are synthesised as graft copolymers or as block polymers. Graft copolymers with a very high proportion of the soft component styrene produce an extremely impact-resistant plastic.
Thermoplastic polyurethane polymers (TPU) are copolymers whose hard component in the form of urethanes is combined with polyethers or polyesters. TPUs are the basis for polyester urethane rubbers.
Polymer blends, also known as polymer alloys, are mixtures of plastics. The polymer blends TPO and TPV include the polyolefin blends. TPOs are non-crosslinked, thermoplastic polymer blends, while TPVs are partially crosslinked blends made of polyolefins.
Production
Thermoplastic elastomers are manufactured by copolymerising two or more monomers by either the graft or the block polymerisation process. While graft polymerisation involves grafting one polymer chain onto another in the form of a branch, block polymerisation produces long-chain molecules with different blocks of hard and soft segments.
In both processes, one of the monomers forms a crystalline or hard segment and acts as a thermally stable component that softens and flows under shear. This behaviour fundamentally differentiates thermoplastic elastomers from thermosetting rubber with its chemical cross-linking between the polymer chains. The other monomer causes an amorphous or soft segment and produces the rubbery properties of TPE.
Because it is possible to precisely adjust the mixing ratios of soft and hard components, materials with very precisely defined properties can be custom-made, for instance in a variety of hardness grades. Fine-tuning can be achieved through the admixture of additives and fillers.
Thermoplastic elastomers are generally produced as granulate for use in conventional injection moulding machines, whereby dyes can be mixed into the compound directly during production.
Properties
Thermoplastic elastomers are characterised by their high reversible elasticity and high flexibility over a very wide temperature range. The materials are also characterised by good strength, impact strength and notched impact strength.
The properties of TPE can be controlled precisely by the lengths of the hard and soft segments as well as the variation of the mixing ratio. This also applies to the chemical resistance. The excellent abrasion resistance speaks in particular for the use of thermoplastic elastomers in surfaces and profiles.
In addition to the chemical behaviour, the hardness, which is measured as “Shore hardness” for plastics, is of decisive relevance for the selection of a thermoplastic elastomer. The range of hardness of thermoplastic elastomers is enormous, starting with 20 to 90 Shore A for very soft gel materials and going up to 85 Shore D, which corresponds to a very hard material.
Chemical resistance
The chemical resistance is determined by the chemistry of the thermoplastic elastomers and their morphology.
Thermoplastic elastomers are characterised by excellent chemical resistance, and good solvent and weather resistance. Another advantage of TPE over thermosetting rubber is its excellent colorability.
Non-polar amorphous TPE materials, such as styrene plastic, have limited chemical resistance to a number of solvents.
The environmental resistance of thermoplastic elastomers is an important requirement, especially in outdoor applications. All TPE groups have some sensitivity to high-energy UV radiation. TPE compounds can be formulated to be ozone-resistant.
Processing techniques
Product designers are increasingly using thermoplastic elastomers, because they can be processed much more cost-effectively and quickly than rubber with conventional thermoplastic systems, as rubber must undergo a chemical cross-linking reaction. This vulcanisation takes between a few minutes and several hours. TPEs do not require this time-consuming cross-linking step and therefore achieve very fast cycle times.
Standard plastic processing methods include extrusion, injection moulding and blow moulding. Thermoplastic elastomers can also be welded.
TPE can be processed in the form of co-injection and co-extrusion with polyolefin and certain engineering plastics, and exhibit excellent bonding with engineering polyamide materials.
The recyclability of materials is becoming increasingly important. TPE processing waste, reject parts or old products can be easily recycled if the different grades are collected separately.