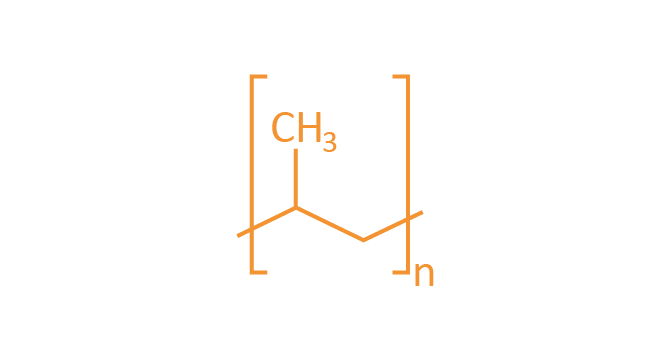
Polypropylene
Polypropylene (PP) is a thermoplastic. It is synthesised by means of a chain polymerisation of propene. The plastic is semi-crystalline and covalent.

Abbreviation
PP
Molecular formula
C3H6 (repeat unit)
CAS no.
9003-07-0
General description
Polypropylene has many similarities to polyethylene, a plastic created by chain polymerisation of ethene, which is a gas very similar to propene. Polypropylene and polyethylene are particularly similar in terms of their electrical properties and solution behaviour. Compared to polyethylene, however, PP has an additional methyl group, which influences some chemical properties and significantly increases the thermal and mechanical resistance. Among standard plastics, PP is the second most commonly used.
Definition
The density of PP is between 0.895 and 0.920 grams per cubic centimetre, so the parts made from it have a very low weight. Polypropylene also has high strength and rigidity. If the plastic is filled with appropriate mineral substances such as talcum or glass fibres, the range of mechanical properties is significantly extended.
Compared to polyethylene, polypropylene has a higher melting temperature. In addition, the maximum temperature to which this plastic can be permanently exposed without becoming unusable is higher. The homopolymer of polypropylene can be used permanently at temperatures between 0 °C and +100 °C. This temperature range can be further increased by copolymerisation.
Production
PP is obtained by polymerising propene, a colorless and odourless gas also known as propylene. Because this polymerisation is a chain reaction, it is often referred to as chain polymerisation. Reactive molecules, so-called monomers, are continuously attached to an ever-growing chain. The final product of such a reaction, composed of several monomers, is called a polymer.
As with ethene, which is used to manufacture polyethylene, propene has a double bond between two of the carbon atoms. This is broken down with the help of a catalyst. Thereby, long chains of carbon and hydrogen atoms are formed.
In the case of polypropylene, a side chain is created, which consists of one carbon and three hydrogen atoms. This is called a methyl group. The way in which such a side chain is arranged is described by means of tacticity.
The tacticity has a significant influence on the properties of the respective polypropylene. The more regular the orientation of the methyl groups, the higher the crystallinity. For this reason, isotactic and syndiotactic polypropylene are partially crystalline, while atactic is amorphous.
Around two thirds of the propene produced worldwide is used to make polypropylene. The commercially available plastic is largely isotactic PP.
Properties
Polypropylene displays great similarity to polyethylene in its properties. However, there are also some differences, which are often due to the additional methyl group of the PP.
Chemical resistance
This factor should also be adequately considered with regard to the proper use of a plastic. Polypropylene is resistant to aqueous solutions of inorganic salts, weak inorganic acids and alkalis, alcohol as well as some oils and solutions of common washing lyes up to 100 °C, among other things.
PP is not resistant to strong oxidising agents. The material swells in aliphatic and aromatic hydrocarbons such as petrol or benzene, especially at elevated temperatures. PP is partially unstable in contact with copper.
Processing techniques
PP is very well suited for injection moulding. The plasticising performance of the injection moulding machine for PP can be very low due to the density.
The melt temperatures are between 200 °C and 270 °C, the mould temperatures between 20 °C and 100 °C. A high temperature results in improved surface gloss.
Spray pressures up to 1200 bar are possible. Nucleating agents significantly increase the crystallisation rate and thus shorten the cycle time. The material has a shrinkage of 1.0 % to 2.5 %.
When extruding PP, extruders with short compression screws should be used. Extrusion blow moulding results in hollow bodies with high dimensional stability under heat. In stretch blow moulding, the processor can achieve increased strength by biaxial stretching.