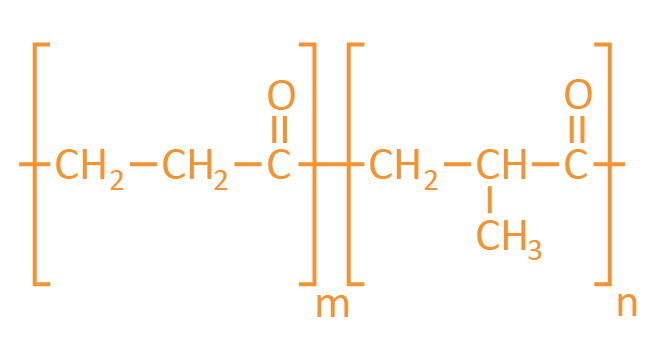
Polyketone
Polyketones (PK) are thermoplastic high-performance polymers with high impact strength, low wear, good solvent resistance and low water absorption. The good environmental compatibility rounds off the positive properties of this versatile material.

Abbreviation
PK
Molecular formula
-
CAS no.
88995-51-1
General description
Polyketone is very resistant to solvents, has excellent barrier properties and excellent mechanical behaviour with convincing tribology. The creep tendency of the semi-crystalline material is very low. Polyketone is elastic and can be deformed reversibly.
The mechanical properties of a component made of PK remain constant even at changing temperatures. Aliphatic polyketones are relatively easy to synthesise compared to other engineering plastics and can be obtained with low resource input.
The moisture absorption is below 0.5%. This hardly affects the mechanical properties. The chemical resistance of PK is outstanding. Polyketone easily withstands weak acids, only very strong acids or alkalis attack the chain structure.
Definition
The polar ketone groups in the polymer main chain of the thermoplastic high-performance polymer significantly determine the properties and are responsible for the naming of polyketone (PK). The strong attraction of the polar ketone groups results in the high melting point of 220 °C of the material.
Molecular symmetry and flexible chains yield good crystallisation, resulting in many beneficial properties such as low wear, high elasticity, high impact strength, high tensile strength, good barrier properties and short cycle times.
Production
Compared to many other engineering plastics, aliphatic polyketones are relatively easy to synthesise. For example, the ethylene carbon monoxide copolymer is coated with a palladium(II) catalyst. This polymer is industrially synthesised either as methanol suspension or via a gas-phase reaction with immobilised catalysts.
Properties
The versatile use of the semi-crystalline material results from the excellent properties of PK:
High resilience
Low moisture absorption
Excellent tribology
Good chemical resistance
Good hydrolysis resistance
Short cycle times
Chemical resistance
Polyketone shows excellent media resistance and can easily withstand weak acids, which attack or even destroy many polyamide grades. Very strong acids or alkalis are required to attack the chain structure. For example, after storage in 30 % sulphuric acid or battery acid or 10 % hydrochloric acid, only slight discolouration of the surface can be observed even after 30 days, while the elongation at break remains practically unchanged.
The hydrolysis resistance of polyketone is excellent, which certifies the material's suitability for applications such as water tanks - an application that was usually realised with polyamide in the past.
PK possesses a high barrier effect against most low-molecular weight media such as oxygen or fuels. In addition, the water absorption of the material is at less than 0.5 %.
Processing techniques
Polyketone is primarily used in injection moulding and crystallises fairly quickly. It is therefore possible to decrease the cycle time and increase productivity during production accordingly. PK compounds are produced non-reinforced and glass fibre or carbon fibre reinforced as well as tribologically modified.
Extrusion processes make it possible to produce high-precision profiles. The common connection technology for PK is welding, for example in the form of laser welding or infrared welding.