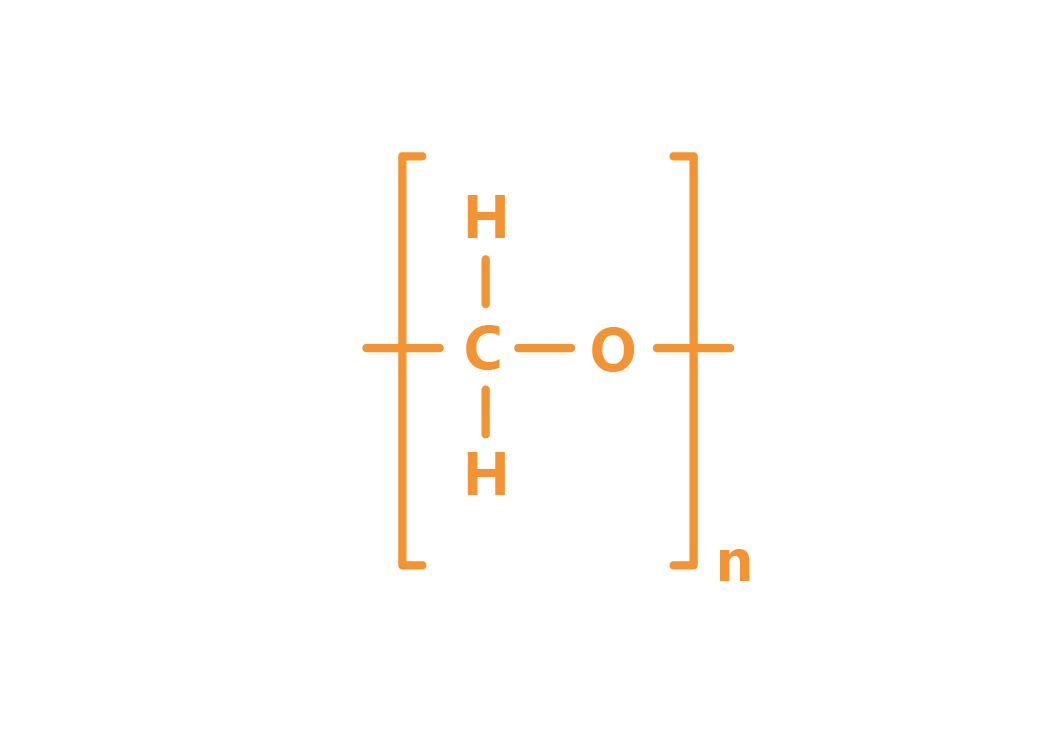
Polyamide
Polyamides (PA) are a group of semi-crystalline polymers known for their wide range of applications in the plastics industry. Every type of PA has a unique chemical structure due to variations in the arrangement of the monomers.
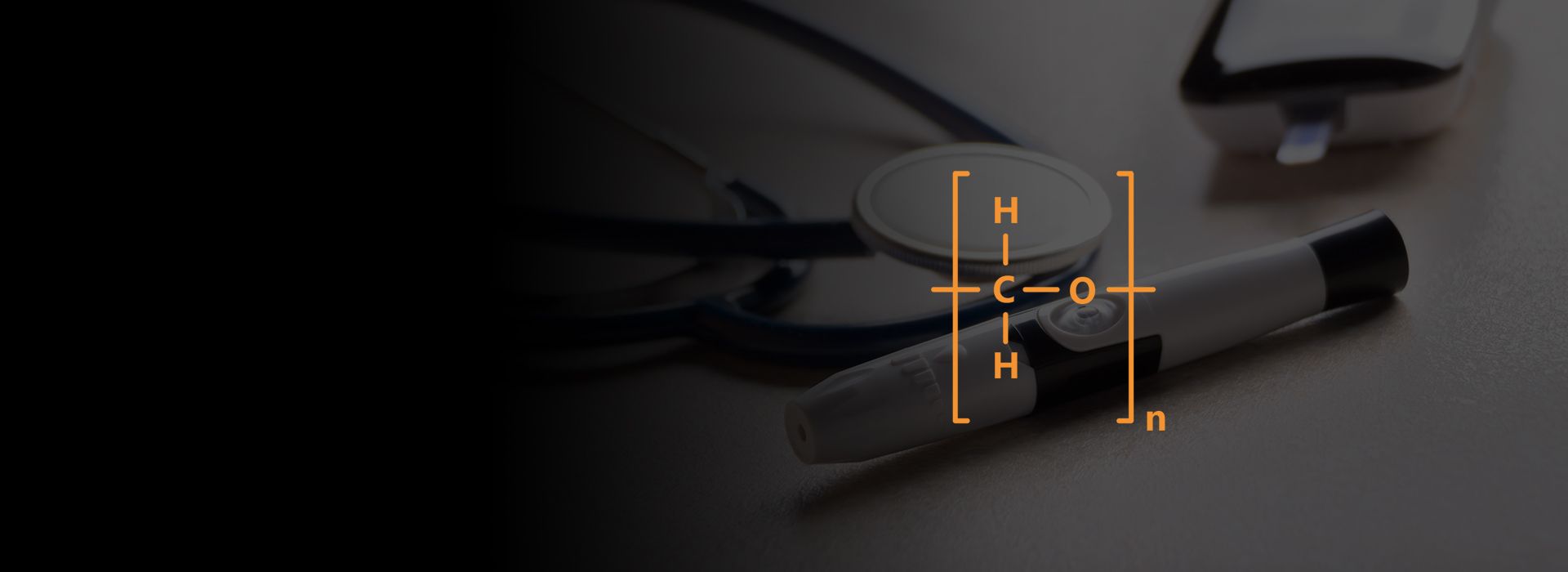
Abbreviation
PA 6 / 6.6
Molecular formula
(C6 H11 NO)n / (C12 H22 N2 O2)n
CAS no.
25038-54-4 / 32131-17-2
General description
Polyamides are versatile synthetic polymers with excellent properties. They are characterised by high strength, toughness and resistance to chemicals and high temperatures. PA is available in several different forms, including PA 6, PA 66, PA 6.10 and PA 6.12, each of which has unique properties and applications. They are used in the automotive, electrical and electronics, aerospace, medical, packaging and food industries, and others. Polyamides (PA) have proven to be vital materials in various industries and applications around the world under a wide range of conditions.
Definition
Polyamides (PA) are a fascinating group of synthetic polymers with a unique chemical structure. This structure consists of alternating amide groups (-CONH-) and alkyl chains. The length of the alkyl chains varies from PA type to PA type. This variation in the length of the alkyl chains has a significant impact on the physical, thermal and mechanical properties of the polyamides. Depending on the length of the alkyl chains, polyamides can have different melting points, strengths, moisture absorption and elasticities.
The variation in alkyl chain length is a key factor in the wide range of properties and applications these materials offer: from textiles to engineering plastic parts to high-performance aerospace applications. The diversity of polyamides is reflected in their chemical structure.
Production
Production of PA 6:
Monomer: The initial substance for the production of polyamide 6 is caprolactam, a ring-shaped monomer with six carbon atoms.
Polymerisation: Caprolactam is first heated to a liquid intermediate and then polymerised under pressure at an elevated temperature. In the process, the ring of the caprolactam opens and the molecules join together to form long chains that constitute the polymer structure of nylon 6.
Processing: The nylon 6 obtained in this way can be further processed in various forms such as fibres or plastic pellets for different applications
Production of PA 6.6:
Monomers: Nylon 66 is made from two monomers: hexamethylene diamine and adipic acid. These two monomers react with each other to form the nylon 66 polymer chain.
Polymerisation: Hexamethylenediamine and adipic acid are mixed and polymerised under heat. During this process, amide bonds form between the monomers, creating the nylon 66 polymer chain.
Processing: The resulting nylon 66 is processed into granules, which are further processed in various industrial processes into end products such as fibres, films, injection-moulded parts, etc.
Properties
Strength: Both PA types have a high tensile strength, which makes them robust and resilient.
Toughness: They are very tough and can absorb impacts and mechanical loads well.
Processability: They are relatively easy to process, which makes them suitable for various manufacturing processes such as injection moulding and extrusion.
Chemical resistance: Both types are resistant to many chemicals, making them suitable for applications in environments with most chemicals.
Insulation properties: They have good insulation properties and are used in electrical applications.
Temperature resistance: Both types can withstand high temperatures without losing their strength or shape.
Flame retardancy: Under certain conditions, both PA 6 and PA 6.6 can have flame retardant properties and help slow or prevent the spread of fires.
Recyclability: PA 6 and PA 6.6 can be recycled and reused.
Chemical resistance
PA 6 and PA 6.6 have good to moderate chemical resistance to many common chemicals. This means that they can come into contact with various substances without immediately changing their properties significantly or dissolving. This makes them useful for a variety of applications where they may come into contact with liquids or gases.
Aliphatic hydrocarbons: resistant
Alcohols, ketones: resistant
Petrol, oils, lubricants: resistant
Hydrocarbons (aromatic): resistant
Hydrocarbons (cyclic): resistant
Tetrachloroethene: resistant
Trichloroethene: resistant
Amines, ammonia: limited resistance
Organic acids (weak): limited resistance
UV radiation: limited resistance
Water (hot): limited resistance
Alkaline solutions: not resistant
Mineral acids: not resistant
Organic acids (strong): not resistant
Processing techniques
PA 6 and PA 6.6 are usually processed by injection moulding and extrusion. These techniques enable the production of a wide range of products, from plastic parts to fibres and filaments.
Injection moulding: This is the most common process for making plastic parts from PA 6 and PA 6.6, where the material is melted and injected into a mould where it cools and solidifies.
Extrusion: This process is used to produce endless profiles, films, pipes and fibres. In this process, the molten material is pressed through a nozzle and shaped.