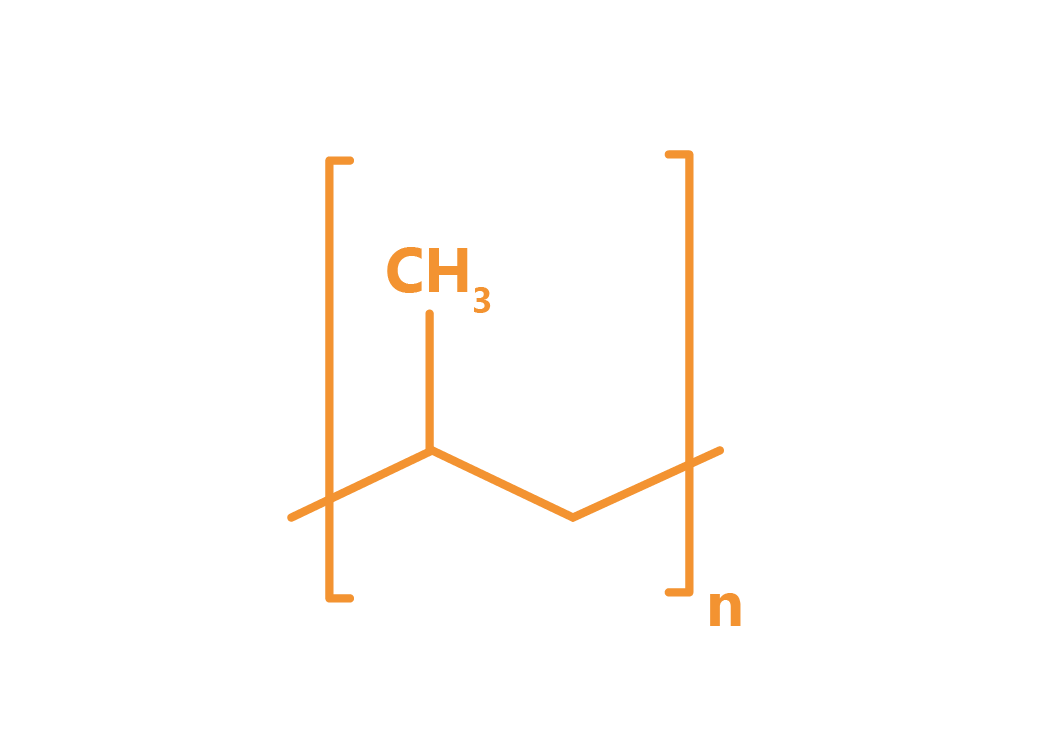
Long fibre-reinforced compounds
Long fibre reinforced compounds (LFRT) are thermoplastics with incorporated reinforcing fibres, which are characterised by a low creep tendency and exceptionally high impact strength or energy absorption due to the greater fibre length.

Abbreviation
LFRT
Molecular formula
-
CAS no.
-
General description
High specific stiffness combined with low weight is one of the most important material properties, especially for structural and load-bearing technical applications. By incorporating reinforcing fibres that are longer than common fibres, impressive strength and stability can be achieved.
Long fibre reinforced compounds (LFRT) are made from a range of semi-crystalline or amorphous thermoplastics as well as various fibres of aramid, carbon, glass or stainless steel. Production is by pultrusion, a strand-drawing process for the continuous manufacture of fibre-reinforced plastic profiles.
Definition
Long-fibre reinforced compounds (LFRT) are thermoplastics that have incorporated reinforcing fibres with a fibre length of 10 millimetres as standard.
Compared to short-fibre-reinforced thermoplastics, LFRTs are characterised by high impact strength and stiffness with a very low creep tendency, which enables the use of this type of fibre-reinforced plastic with increased quality requirements.
Compared to fibre-reinforced duromers, long-fibre-reinforced compounds have higher toughness, a lower level of emissions during processing, better recyclability, lower cycle times and an almost unlimited shelf life.
Production
Long-fibre-reinforced thermoplastic components are manufactured using compression or injection moulding processes. The fibres are incorporated into the polymer matrix by pultrusion or in a direct process.
Properties
LFT with a considerably longer fibre length have significantly better mechanical properties than comparable fibre composite plastics with short fibres. Amongst other things, they are characterised by high impact strength, good creep resistance and very good stability in a wide temperature range and under variable climatic conditions. Compared to conventional short fibre-reinforced materials, the longer fibres have a skeletal structure that limits anisotropic shrinkage and greatly reduces the tendency of the parts to warp.
In addition to the required structural integrity, corrosion resistance and low weight, long fibre-reinforced compounds meet all the necessary requirements for use as a metal substitute.
Chemical resistance
Depending on the round polymer, LFRTs have good chemical resistance to lubricants, fuels, water vapour, cleaning agents and preservatives.
In addition, LFRT are insensitive to environmental influences such as salt water. This makes long-fibre-reinforced compounds particularly suitable for applications in automotive and aircraft construction.
Processing techniques
The extruded material or semi-finished products produced in the direct process are processed by injection moulding or pressing. The press process, which is mainly used for flat components, has the advantage of shorter cycle times and longer fibre lengths, which result in better mechanical properties. However, press burrs occur during pressing, which means that post-processing is necessary.
With injection moulding, a better surface quality can be achieved. In addition, it is possible to incorporate inserts directly. The design freedom is thus much higher compared to pressing.