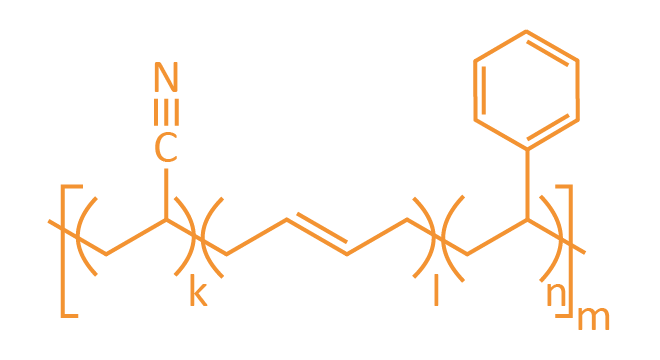
Acrylonitrile butadiene styrene copolymer
The amorphous polymer ABS is widely used due to its dimensional stability, good impact strength, excellent colourability, high gloss, versatile finishing options and convincing price-performance ratio.

Abbreviation
ABS
Molecular formula
(C8H8·C4H6·C3H3N)n
CAS no.
9003-56-9
General description
In addition to the household and consumer goods industry, the material is extremely popular in the automotive and electronics industries. Additives can be used to specifically optimise the properties of the material for a wide range of product applications. The material is completely recyclable.
In the field of prototype production, the amorphous plastic convinces with its easy processing, high stability, good chemical and heat resistance as well as flexibility in post-processing: painting, galvanising, printing, grinding, gluing or filling are possible without any problems.
Due to its convincing properties, the material is a proven starting material in 3D printing.
Definition
Acrylonitrile-butadiene-styrene belongs to the group of amorphous polymers and impact-resistant engineering thermoplastics. ABS polymers are composed of the three monomers acrylonitrile, butadiene and styrene and are therefore also called terpolymers.
Acrylonitrile is a synthetic monomer whose production is based on propylene and ammonia. Acrylonitrile contributes to heat resistance and chemical resistance. Butadiene is produced as a by-product of ethylene production. Butadiene gives the polymer its excellent impact strength and toughness.
Styrene is produced by dehydrogenating ethylbenzene and is responsible for the stiffness and good processability.
Production
It is produced by the emulsion process or the continuous mass process. The material has an opaque ivory colour and can easily be mixed with pigments or coloured with dyes.
ABS can be classified between the standard polymers (PVC, polyethylene, polystyrene, etc.) and the technical polymers (polybutylene terephthalate, polamide, polyacetal, etc.) and guarantees a good price-performance ratio.
Properties
ABS is characterised by excellent mechanical properties as it is naturally hard, tough and therefore offers good impact resistance. The terpolymer has a high level of surface quality as well as good electrical insulation properties. The material is chemically and heat resistant. However, the material is easily attacked by polar solvents.
The pure material is fully recyclable and is non-toxic, harmless and stable in terms of biocompatibility. It is possible to mix recycled ABS with new material in order to manufacture products in the most resource-friendly way possible at lower costs without compromising on quality. By adding additives or varying the ratio of the three monomers acrylonitrile, butadiene and styrene, a variety of ABS types with optimised properties can be produced. The additives include, for example, UV stabilisers, heat stabilisers, lubricants or hydrolysis stabilisers.
The ABS grades produced are available in qualities with improved impact strength, increased heat resistance and improved galvanisability, among others. ABS mixed with fibres, fillers or minerals results in grades with improved stiffness, impact strength and dimensional stability.
Chemical resistance
ABS has very good resistance to dilute acids and alkalis, water and aqueous salt solutions as well as saturated hydrocarbons such as petrol. The same applies to mineral oils and animal and vegetable fats. The resistance to aliphatic hydrocarbons is moderate. The material shows poor resistance to aromatic and chlorinated hydrocarbons, to esters, ethers and ketones as well as alcohols and concentrated mineral acids.
The weather resistance of the natural material is moderate. By galvanising the material with an adhesive metal layer, by pigmentation and by additional UV stabilisation, the weather resistance can be greatly improved. The material is one of the most important plastics in the field of galvanisation.
Processing techniques
Processing of the terpolymer acrylonitrile-butadiene-styrene is simple and possible on most standard machines. ABS can be injection moulded, blow moulded or extruded. Because the melting temperature is low, the material is particularly suitable for processing in 3D printing on an FDM machine. The material can be easily coated with metals by electroplating. This allows product surfaces to be refined, for instance, by chrome plating.
Thermoformed parts made of the material are often used. Examples include foils and sheets, electronic and automotive parts, housings for computers and electrical appliances, toys, motorbike helmets or edge bands for furniture.
In 3D printing, the material is used as a filament and impresses with its high stability and excellent post-processing possibilities. Painting, coating, sanding, gluing or filling are possible without problems. The copolymer is thus often the material of choice for the production of prototypes.