Engineering Plastics
Technical support
Sustainability
Locations
Downloads
Image dimensions not found
Change image or reupload it
About us
Worldwide success since 70 years
We are your partner when it comes to the distribution of high-quality engineering plastics.
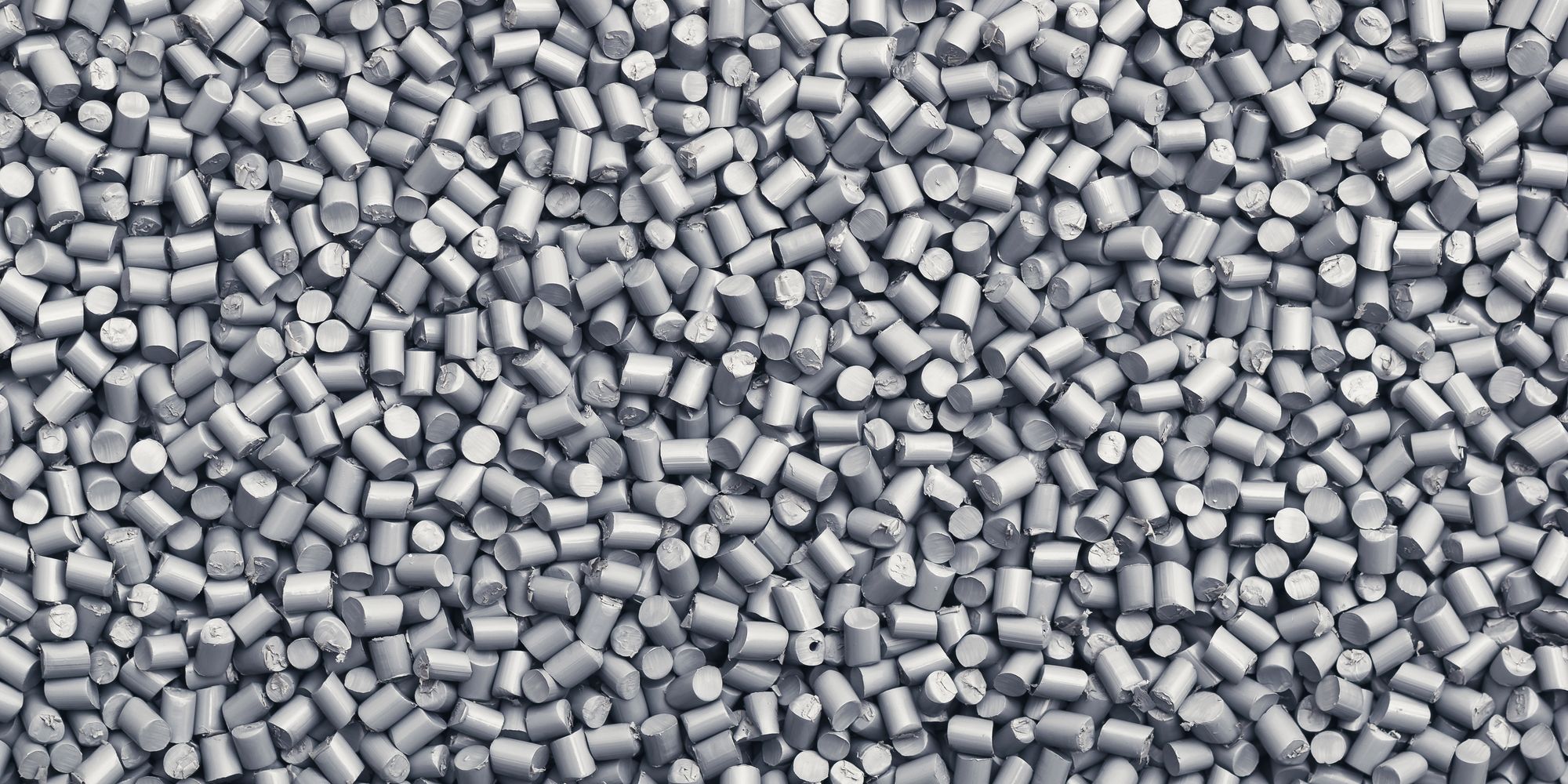
Products
Our products and polymers
We distribute a wide range of engineering plastics from polypropylene to polyketones. To ensure that we always meet our customers' needs, we work closely with leading international plastics producers.